Skid steers are among the most versatile and in-demand pieces of equipment in any rental fleet. Their compact design, maneuverability, and compatibility with numerous attachments make them essential for construction, landscaping, agriculture, and demolition projects.
For equipment rental businesses, choosing the right skid steer brands and models is critical for maximizing fleet utilization, customer satisfaction, and return on investment. With numerous manufacturers, specifications, and price points, making an informed decision requires understanding both the equipment and your specific rental market needs.
In this comprehensive guide, we’ll analyze the top skid steer brands based on reliability, performance, maintenance requirements, and rental profitability. Our recommendations are based on industry data, rental operator feedback, and long-term ownership costs that directly impact your bottom line.
The Top 5 Skid Steer Brands for Equipment Rental
When selecting skid steers for your rental business, reliability, parts availability, ease of maintenance, and customer demand should be your primary considerations. These top five manufacturers consistently deliver on these criteria while offering features that renters value.
Bobcat
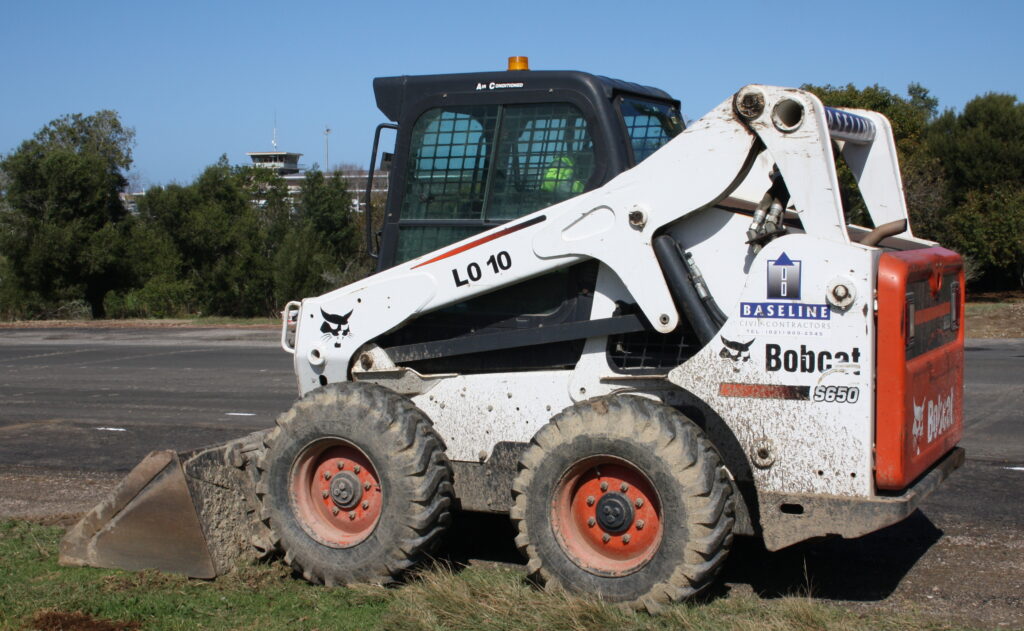
Market Position: Bobcat dominates the skid steer market with approximately 40% market share, making it the most recognized brand among contractors and DIY renters alike. This brand recognition translates to higher rental demand and utilization rates.
Company Background: Originally Melroe Manufacturing, Bobcat pioneered the first true skid steer loader in the 1960s and has maintained its leadership position through continuous innovation.
Key Models for Rental Businesses:
- S70 (Compact): Ideal for tight-space applications with a 23.5 HP engine and 760 lb rated operating capacity. This entry-level model is perfect for homeowner rentals and light-duty applications.
- S650 (Mid-Size): The workhorse of many rental fleets with a 2,690 lb operating capacity and 74 HP engine. Its versatility makes it the most frequently requested size for general construction applications.
- S850 (Large): With a 3,950 lb operating capacity and 100 HP engine, this larger model meets the needs of heavy construction contractors and commands premium rental rates.
Rental Business Advantages:
- Highest customer recognition and demand
- Extensive dealer network for parts and service
- User-friendly controls that require minimal training for renters
- Advanced features like touch displays, best-in-class lift capacity, and strong hydraulics systems
Maintenance Considerations: Bobcat machines typically require service after every 50 hours of operation, with major maintenance recommended at 500-hour intervals. The newer M-Series features improved serviceability with easier access to routine maintenance points.
ROI Factors: While Bobcat machines command a higher initial investment (typically 10-15% above industry average), they deliver superior rental utilization rates and stronger resale values, making them an excellent long-term investment for rental operators.
Caterpillar
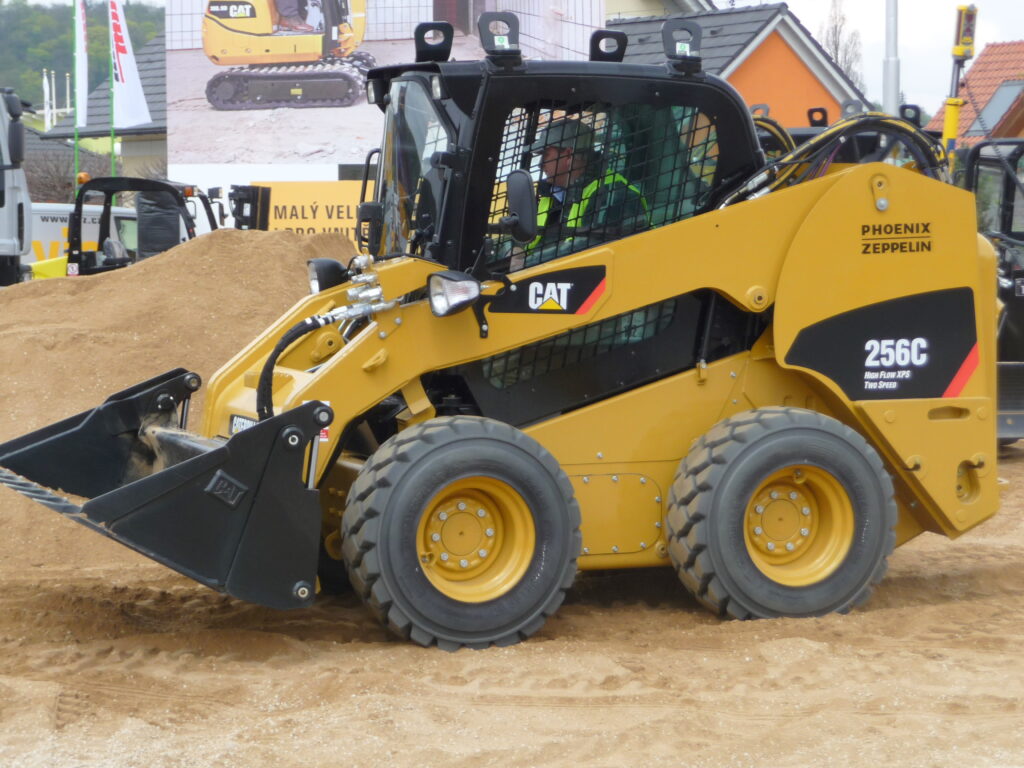
Market Position: Caterpillar holds approximately 18-20% of the skid steer market, leveraging its reputation as the premium brand in heavy construction equipment to establish a strong presence in the skid steer segment.
Company Background: Caterpillar entered the skid steer market in 1999, bringing its century of construction equipment expertise to this growing product category. Despite being a relative latecomer, Cat has quickly established itself as a premium option.
Key Models for Rental Businesses:
- 226D3 (Compact): With 67.1 HP and 1,550 lb rated operating capacity, this entry-level model provides excellent maneuverability while maintaining the Cat reputation for durability.
- 262D3 (Mid-Size): Offering 74.3 HP and 2,700 lb operating capacity, this versatile model is ideal for diverse rental applications from landscaping to construction.
- 272D3 (Large): The flagship model with 98 HP and 3,700 lb operating capacity, designed for heavy-duty applications and capable of running virtually any attachment.
Rental Business Advantages:
- Superior hydraulic performance and industry-leading lifting capacity
- Electric throttle control and high-flow hydraulic options
- Excellent visibility and operator comfort reducing fatigue
- Exceptional ground clearance for varied job site conditions
- Parts commonality with other Cat equipment potentially in your fleet
Maintenance Considerations: Caterpillar equipment features easy service access with rear-tilting cabs and grouped service points. The D3 series machines require 500-hour service intervals with daily fluid checks, reducing downtime compared to some competitors.
ROI Factors: Caterpillar skid steers command the highest initial investment among competitors (15-20% premium), but offer strong residual values, typically retaining 60-65% of their value after three years. Their premium position also allows for higher rental rates in most markets.
CASE
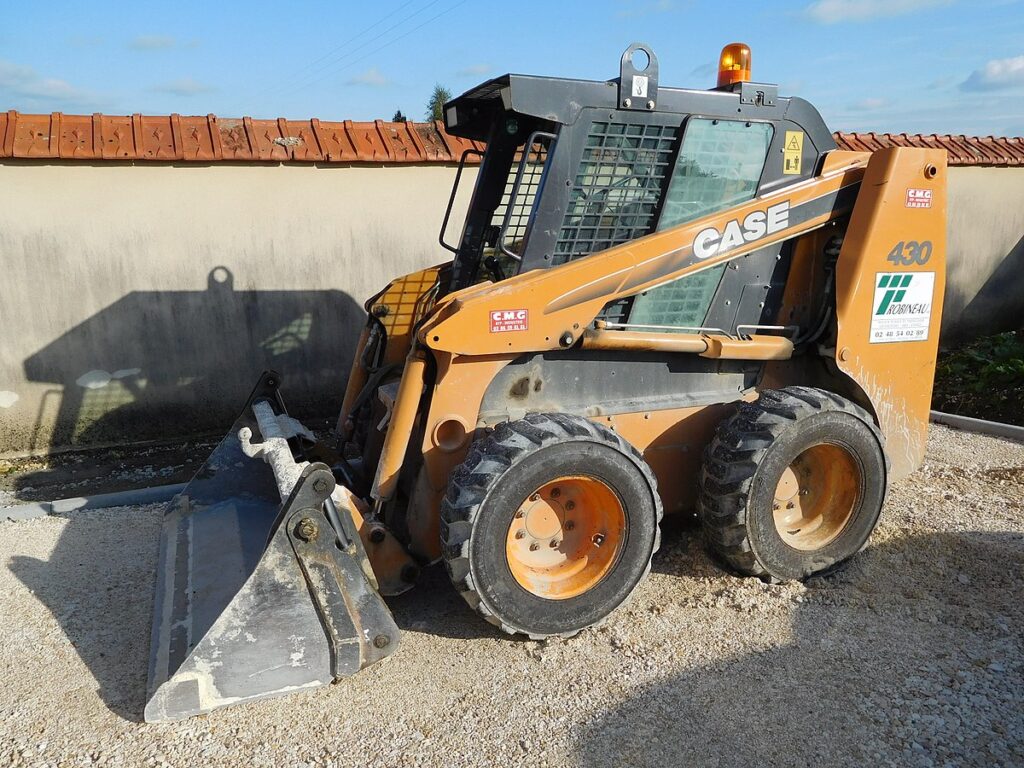
Market Position: CASE holds approximately 15% of the skid steer market, positioning itself as a value-oriented alternative to premium brands while maintaining professional-grade build quality.
Company Background: CASE has been producing skid steers since 1969, giving them over five decades of experience. The company merged with New Holland in 1999, creating CNH Industrial, but maintained separate brand identities and distribution networks.
Key Models for Rental Businesses:
- SR160 (Compact): With 60 HP and 1,600 lb operating capacity, this model offers an excellent entry point for rental fleets needing a reliable compact option.
- SV280B (Mid-Size): This 74 HP machine with 2,800 lb operating capacity features vertical lift design, making it ideal for loading applications in construction and landscaping.
- SV340B (Large): The largest model with 90 HP and 3,400 lb operating capacity, designed for heavy material handling and attachment-intensive applications.
Rental Business Advantages:
- Competitive acquisition cost (typically 5-10% less than Bobcat and Cat)
- Superior visibility with low threshold and skylight
- Industry-leading breakout force
- Simple, intuitive controls that reduce customer training time
- Good parts availability through CNH dealer network
Maintenance Considerations: CASE skid steers feature tilt-up cabs for maintenance access and grouped service points. The B-Series models offer extended 500-hour service intervals on hydraulic oil and filters, reducing maintenance expense and downtime.
ROI Factors: CASE offers a strong value proposition with lower initial costs than premium brands while maintaining good residual value (typically 50-55% after three years). These machines often achieve rental ROI 2-3 months sooner than premium brands due to the lower acquisition cost.
John Deere
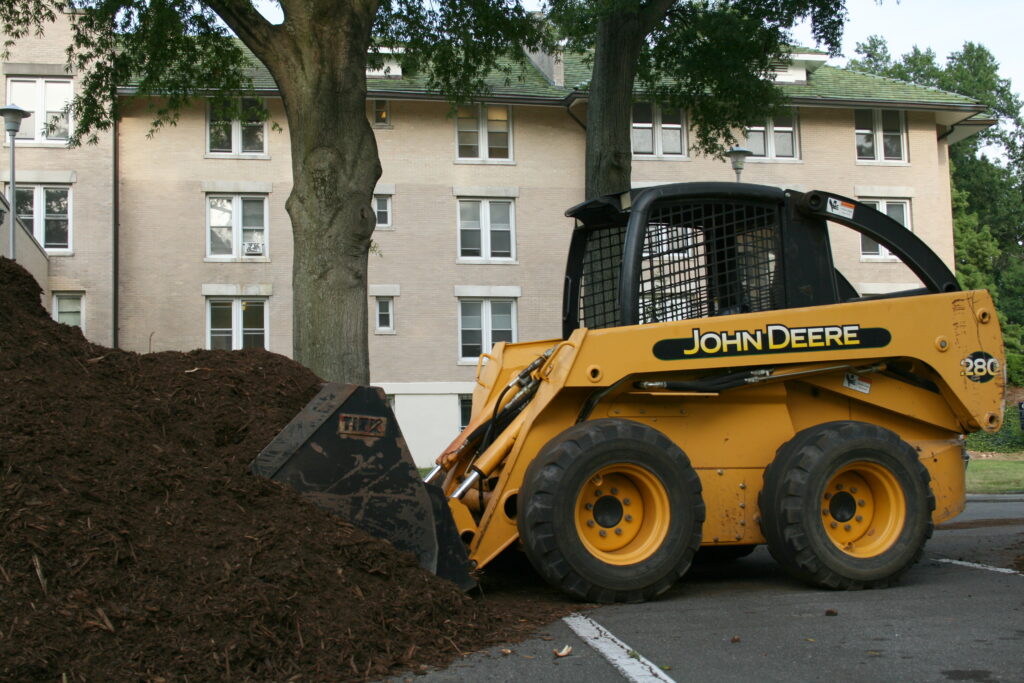
Market Position: John Deere commands approximately 12% of the skid steer market, leveraging its strong reputation in agricultural equipment to serve both farm and construction rental customers.
Company Background: While primarily known for farming equipment, John Deere has been producing construction equipment for decades. Their skid steer line benefits from the company’s extensive experience with hydraulic systems and drivetrain components.
Key Models for Rental Businesses:
- 318G (Compact): With 65 HP and 1,800 lb operating capacity, this versatile machine is ideal for landscape contractors, builders, and agricultural applications.
- 324G (Mid-Size): This 74 HP model with 2,690 lb rated capacity offers excellent power-to-weight ratio and serves as a versatile all-purpose machine for rental fleets.
- 332G (Large): With 100 HP and 3,600 lb operating capacity, this machine excels in heavy material handling and excavation applications where premium performance justifies higher rental rates.
Rental Business Advantages:
- Exceptional hydraulic performance for attachment-intensive applications
- Vertical lift models provide excellent reach at full height
- Cab comfort and visibility reduce operator fatigue
- Strong dealer network with agricultural crossover for rural rental operators
- Compatibility with many of the same attachments used on Deere agricultural equipment
Maintenance Considerations: John Deere skid steers feature swing-out rear doors and tilt-up cooling packages for easy access to maintenance points. The G-Series requires 500-hour service intervals, with convenient grouped service points that reduce maintenance time.
ROI Factors: John Deere skid steers command a price premium (10-15% above average), but offer excellent residual value, typically retaining 55-60% after three years. They particularly excel in mixed-use rental markets where agricultural applications are common.
JCB

Market Position: JCB claims approximately 10% of the global skid steer market, differentiating itself through innovative side-entry design and strong presence in international markets.
Company Background: JCB entered the skid steer market with a revolutionary approach, eliminating the traditional front entry in favor of a side door. This design change addresses safety concerns related to operators having to step over attachments.
Key Models for Rental Businesses:
- 155 (Compact): With 60 HP and 1,550 lb operating capacity, this compact model offers the unique side-entry design in a small package perfect for tight spaces.
- 215 (Mid-Size): This 74 HP machine with 2,100 lb capacity balances power and agility, making it ideal for general-purpose rental applications.
- 3TS-8W (Large): With 74 HP and 3,186 lb capacity, this teleskid model combines skid steer maneuverability with telescopic boom capability, offering rental customers unique functionality.
Rental Business Advantages:
- Side-entry design improves safety and reduces potential liability
- Single-arm PowerBoom provides 270° visibility compared to 165° in conventional designs
- Spacious cabs (up to 46% larger than competitors) improve operator comfort
- Common engine platform across models simplifies maintenance and parts inventory
- Fuel efficiency up to 15% better than conventional models
Maintenance Considerations: JCB’s side-entry design eliminates the need for tilting cabs, with all service points accessible from ground level. This unique approach reduces maintenance time and simplifies routine servicing, potentially saving 25% in service labor costs.
ROI Factors: JCB offers a competitive initial investment (typically 5-7% less than Bobcat), coupled with strong fuel efficiency and lower maintenance costs. Their unique design commands attention in rental yards and can be a differentiator for rental businesses looking to stand out.
Runner-Up Brands Worth Considering
While the top five brands dominate the market, these runner-up manufacturers offer compelling alternatives that might be worth considering for specific rental business needs or regional markets.
Kubota
Market Position: Known primarily for compact tractors, Kubota has been expanding its construction equipment lineup with well-regarded skid steers that emphasize fuel efficiency and operator comfort.
Key Models for Rental:
- SSV65: A 64 HP machine with 1,950 lb operating capacity that competes well in the mid-size segment
- SSV75: Offering 2,300 lb capacity and 74.3 HP, this model features a wider cab for operator comfort
Rental Business Advantages:
- Lower acquisition cost than premium brands (typically 5-10% less)
- Excellent fuel efficiency (up to 15% better than some competitors)
- Growing dealer network with improving parts availability
Why It’s a Runner-Up: While Kubota makes excellent machines, they have a smaller market share and less brand recognition among renters. Parts availability can be more limited in some regions, potentially increasing downtime if repairs are needed.
New Holland
Market Position: Though part of the same parent company as CASE (CNH Industrial), New Holland positions its skid steers distinctly, with a focus on agricultural customers and applications.
Key Models for Rental:
- L325: With 74 HP and 2,500 lb operating capacity, this versatile machine offers super boom vertical lift design for excellent reach
- L334: Featuring 90 HP and 3,400 lb operating capacity for heavy material handling applications
Rental Business Advantages:
- Strong dealer presence in agricultural regions
- Competitive pricing (typically 7-12% below premium brands)
- Super Boom vertical lift design provides excellent reach and dump height
- Good parts availability through CNH dealer network
Why It’s a Runner-Up: New Holland lacks the brand recognition of top-tier manufacturers in construction applications, potentially leading to lower demand in urban rental markets. Their machines are excellent but have more limited market awareness outside agricultural settings.
Gehl
Market Position: As one of the pioneers in the skid steer industry, Gehl maintains a loyal following, particularly among experienced operators and in rural markets.
Key Models for Rental:
- R190: A 69 HP machine with 1,900 lb operating capacity, ideal for all-purpose rental applications
- V420: Their flagship model with 120 HP and 4,200 lb capacity, one of the largest in the industry
Rental Business Advantages:
- Competitive acquisition cost (often 10-15% below premium brands)
- Robust design with reputation for durability
- Simplified mechanical systems reduce complexity and maintenance costs
- V-Series vertical lift models offer excellent reach and lift height
Why It’s a Runner-Up: Gehl’s relatively limited dealer network compared to major brands can make parts availability challenging in some regions. While the machines themselves are reliable, the potential for longer downtime during repairs keeps them from the top tier for rental businesses.
What Is the Best Skid Steer Brand?
Any of the top skid steer brands would be a great choice for your rental business. However, the consensus is that Bobcat makes the best skid steers — as it owns 40% of the total market share. It was the first to introduce skid steers to the market in the 1960s.
Bobcat offers various sizes, including compact models for yard work and larger models for major construction projects. Caterpillar is another reliable name, with a much larger variety of equipment. Both brands are relatively easy to service and experience few breakdowns. However, they are both generally more expensive than other brands.
In the rental industry specifically, Bobcat and Caterpillar dominate because of their strong brand recognition among renters. Many contractors will specifically request these brands by name, which can lead to higher utilization rates for your fleet.
The “best” brand ultimately depends on your rental market, customer base, and business model. Urban rental businesses serving primarily construction contractors may benefit most from Bobcat or Caterpillar’s brand recognition, while rural operations with agricultural customers might find John Deere or New Holland provides better value.
What’s the Best Skid Steer for the Money?
Based on 2025 data and recent industry analysis, JCB continues to offer the best skid steer for the money. The company has maintained its reputation for producing reliable smaller construction machines with excellent value retention. JCB offers the best skid steer for the money. According to the latest EquipmentWatch market report, JCB skid steers retain approximately 58% of their value after three years of ownership, placing them among the industry leaders in this critical metric.
JCB’s side-entry design not only improves safety but has been shown to reduce maintenance costs by approximately 25% compared to traditional designs, according to a 2024 study by the Equipment Management Association. The power offered by JCB skid steers is more than sufficient for most rental applications, plus the controls are modern, and the cabs are roomier than most competitors.
CASE also deserves consideration in the value category, with acquisition costs typically 5-10% below premium brands while maintaining comparable performance specifications. Their B-Series machines offer industry-leading breakout force and simplified maintenance access that can reduce operating costs over time.
So who makes the best skid steer? Bobcat and Caterpillar skid steers are both known for holding their value very well. Overall, the best skid steer to buy will come down to those that fit your major needs, such as lift capacity and reliability.
How to Choose the Right Skid Steers for Your Rental Business
Below are eight key criteria to consider when looking for the best skid steer brand.
Lift Capacity
Lift capacity is how much the skid steer can lift. Skid steers will have one of two lift arm styles: radial and vertical lifts. Vertical lifts are for up-and-down movement versus reach. This option is best for moving heavy pallets or dumping material into trucks.
Radial lifts are good for backfilling and putting materials on flatbed trucks. The bucket can be lifted in an arc, allowing for better range.
For rental businesses, it’s often advisable to maintain a mix of both lift styles in your fleet:
- Vertical lift models typically command higher rental rates and are preferred for loading and material handling
- Radial lift models excel in ground-engaging applications and often cost less to acquire
Reliability
How reliable the equipment is should also be a major factor. You don’t want to spend hundreds of dollars on repairs each month. Instead, it’s better to invest in a high-quality piece of equipment. Additionally, a good maintenance plan will boost the useful life of any skid steer.
Rental businesses should consider:
- Dealer reputation for service and parts availability
- Availability of extended warranty options
- Simplicity of design (fewer electronic components often means fewer potential failure points)
- Brand track record for specific models (some manufacturers have certain models that consistently outperform others)
Available Attachments
The attachments available for the skid steer are also important. A variety of attachments will increase the skid steer’s versatility and make it more marketable for rentals. You should consider the following attachments:
- Pallet forks
- Backhoes
- Brush cutters
- Augers
- Grapples
- Bale spears
- Buckets
- Blades
- Trenchers
The more attachments a skid steer can use, the more projects it can tackle. Some considerations specific to rental businesses include:
- Hydraulic coupler systems that allow for quick attachment changes
- Rental-friendly designs that minimize potential damage points
- Compatibility with attachments already in your fleet
- Availability of attachments from multiple suppliers to control costs
Suitability for Different Project Scopes
How well does the skid steer work for different projects? For example, you might need a skid steer to fit into tight spaces. In that case, look for a compact model. In contrast, bigger loads will require a larger capacity.
For rental businesses, it’s important to understand your market’s typical applications:
- Urban markets typically demand more compact machines for renovation and landscaping
- Rural markets often need larger machines for agricultural and excavation work
- Construction-focused rental businesses benefit from machines with higher lift capacities
- Machines with enclosed cabs and climate control command higher rental rates in extreme weather regions
Type of Hydraulic System
Skid steers come with one of two hydraulic systems: low-flow or high-flow. The flow of the hydraulic system is how hydraulic fluid is moved through two hoses in the skid steer. Low-flow skid steers move less hydraulic fluid per minute than high-flow.
The higher the flow, the more powerful the skid steer, meaning it can use larger attachments, such as snow blowers and stump grinders.
For rental businesses, high-flow hydraulic systems typically:
- Command 15-25% higher rental rates
- Attract professional contractors as customers
- Support more specialized attachments
- Require higher initial investment
Many rental businesses find that a fleet mix of approximately 30% high-flow and 70% standard-flow machines provides the best balance of specialized capability and broad market appeal.
Engine Type
Engine type comes into play when meeting EPA emission requirements; 75-horsepower diesel engines on non-road equipment must be Tier 4 compliant. These engines, however, require additional maintenance to prevent damage. Consistent maintenance and keeping the fuel filters clean can help the engine stay in good working order.
Rental businesses should consider:
- Tier 4 Final compliance requirements for new equipment
- The complexity of emission systems (DEF requirements, regeneration cycles)
- Training requirements for customers unfamiliar with modern diesel systems
- Availability of manufacturer training for your service staff
Costs
For rental businesses, total cost of ownership includes more than just the initial purchase price:
Acquisition Costs:
- Initial purchase price
- Financing terms and interest rates
- Available manufacturer incentives
- Bundling opportunities for fleet purchases
Operational Costs:
- Fuel consumption
- Routine maintenance expenses
- Parts availability and pricing
- Labor rates for specialized service
Ownership Costs:
- Insurance premiums
- Expected downtime
- Residual value after your typical ownership period
- Warranty coverage
Most rental businesses find that premium brands with higher initial costs often deliver better long-term returns through stronger residual values, higher rental rates, and better utilization. A typical rule of thumb is that a skid steer should pay for itself within 24-30 months of rental service.
Dealer Availability
The proximity and quality of dealer support is particularly critical for rental businesses:
Service Availability:
- Emergency repair response times
- Mobile service capabilities
- Availability of loaner equipment during extended repairs
Parts Inventory:
- Stock levels of common wear items
- Overnight parts availability
- Cross-compatibility with other equipment in your fleet
Training Support:
- Technician certification programs
- Operator training resources for your staff and customers
- Diagnostic equipment and software access
Relationship Factors:
- Dealer financial stability
- Willingness to provide preferred customer status
- History with other rental businesses
The ideal dealer relationship includes priority service scheduling for rental businesses and parts availability guarantees to minimize downtime—two factors that can significantly impact your rental operation’s profitability.
Should You Buy a Used Skid Steer for an Equipment Rental Business?
For rental businesses looking to maximize ROI, the question of new versus used equipment is always relevant. Used skid steers can offer significant upfront savings, but come with important considerations:
Pros of Used Skid Steers:
- Lower Initial Investment: Used skid steers typically cost 40-60% less than new models
- Reduced Depreciation: New equipment experiences the steepest depreciation in the first 2-3 years
- Potentially Faster ROI: Lower acquisition costs can mean quicker break-even points
- Viable Fleet Expansion Strategy: Allows for broader equipment offerings with less capital
Cons of Used Skid Steers:
- Higher Maintenance Costs: Older machines typically require more frequent repairs
- Less Attractive to Renters: Some customers prefer newer equipment with modern features
- Limited Warranty Coverage: Used equipment typically comes with limited or no manufacturer warranty
- Unknown History: Previous abuse or poor maintenance can lead to reliability issues
- Customer Perception: Some rental customers associate used equipment with lower-tier rental operators
Best Practices When Buying Used:
- Focus on Low-Hour Machines: Look for skid steers with under 2,000 hours for the best balance of value and remaining useful life
- Stick with Tier 1 Brands: Bobcat, Caterpillar, and other top brands typically hold up better over time
- Request Maintenance Records: Documented service history indicates a well-maintained machine
- Consider Dealer-Certified Used Equipment: These often include inspections and limited warranties
- Factor in Compliance Requirements: Ensure older machines meet current emissions standards for your region
- Perform Comprehensive Inspections: Check hydraulic systems, undercarriage components, and operational functions thoroughly
The Financial Equation:
For rental businesses, a good rule of thumb is that a used skid steer should cost no more than 60% of a new model’s price if it has 2,000-3,000 hours. For each additional 1,000 hours, deduct approximately 10% from the value.
The sweet spot for many rental operations is acquiring 2-3 year old machines from contractors who typically upgrade at this interval, allowing you to capture significant savings while still offering modern, reliable equipment to your customers.
Many successful rental businesses implement a hybrid approach: premium, low-hour new machines for demanding applications and well-maintained used units for general-purpose work. This strategy maximizes capital efficiency while maintaining a competitive rental offering.
Managing Your Skid Steer Fleet with Rental Software
Acquiring the right skid steers is only half the battle for rental businesses. Effective fleet management is critical for maximizing utilization, tracking maintenance, and optimizing rental rates.
Modern rental management platforms like Quipli help equipment rental businesses:
- Track Utilization and Profitability: Monitor which skid steer models and sizes are performing best in your fleet, including detailed metrics on revenue per asset, time utilization, and maintenance costs to identify your most profitable units.
- Schedule Preventative Maintenance: Set automatic maintenance reminders based on engine hours or calendar intervals, ensuring your skid steers receive timely service to extend their operational life and minimize costly repairs.
- Manage Attachments: Track which attachments are rented with each skid steer to identify complementary rental opportunities and create bundled packages that increase average transaction value.
- Optimize Rental Rates: Analyze seasonal demand patterns to implement dynamic pricing strategies that maximize revenue during peak periods while maintaining competitive rates during slower seasons.
- Streamline Customer Experience: Allow customers to browse available skid steers, view specifications, and book online 24/7, creating a modern rental experience that differentiates your business from competitors.
By combining the right fleet selections with powerful rental management software, your skid steer fleet can become one of your most profitable equipment categories. The data from your rental software can also inform future purchasing decisions, helping you build a fleet that precisely matches your market’s demand patterns.
Ready to Add a Skid Steer to Your Rental Portfolio?
The five skid steer brands above represent the gold standard for equipment rental fleets, with the runner-up options providing viable alternatives for specific scenarios. Regardless of which manufacturer you choose, skid steers remain one of the most versatile and in-demand pieces of equipment in the rental industry.
Making the most out of your rental business is the goal of the Quipli team. We provide an automated system for managing your rental inventory and scheduling, allowing you to focus on strategic fleet decisions rather than administrative tasks.
That’s why we’ve put together an all-in-one equipment rental software, designed to help you grow and manage your business. Reach out today for a demo to see how Quipli can help you optimize your skid steer fleet and maximize your rental ROI.